What is the Injection Molding Process? A Comprehensive Guide
Injection molding is one of the most widely used manufacturing processes in modern industries. It’s a versatile technique used for producing parts in a variety of materials, from plastics to metals. In this blog, we’ll explain the injection molding process step by step, highlight its key benefits, and why it’s crucial for manufacturing industries like automotive, electronics, medical devices, and more.
1. What is Injection Molding?
Injection molding is a manufacturing process used to create parts by injecting molten material into a mold. This process is especially popular for producing plastic parts, but can also be used for other materials like metals, glass, and elastomers. The injection molding process is highly efficient, producing large quantities of identical parts with precise shapes, fine details, and uniform quality.
2. The Injection Molding Process: A Step-by-Step Overview
Step 1: Mold Design and Preparation
Before the injection molding process begins, the mold needs to be designed and created. Molds are typically made from steel or aluminum and are carefully crafted to match the desired part's shape and design. The mold is divided into two parts: the cavity (where the material is injected) and the core (which forms the part’s shape). Precision is key to ensuring that parts come out with minimal imperfections.
Mold Design & Molding Simulation
Step 2: Material Selection
The right material needs to be selected based on the part’s desired properties. Plastics like ABS, polyethylene (PE), polypropylene (PP), and polystyrene (PS) are commonly used, but specialized materials can be chosen for applications such as medical devices, automotive parts, and consumer electronics.
Step 3: Melting the Material
In the injection molding machine, the raw material (usually in the form of pellets) is fed into a heated barrel where it’s melted. The material is heated to the optimal temperature, turning it into a liquid that can be injected into the mold.
Step 4: Injecting the Material
Once the material is melted, it’s injected into the mold cavity using high pressure. The injection mold is precisely controlled to ensure that the material fills every corner of the cavity without air pockets, which could cause defects in the final part.
Step 5: Cooling
After the molten material has filled the mold, the mold is cooled. The cooling time varies depending on the material used and the part's size. The cooling process solidifies the material into the shape of the mold.
Step 6: Ejection
Once the part has cooled and solidified, it’s ejected from the mold. This is typically done using ejector pins or plates. The mold opens, and the finished part is removed.
A high-precision medical part was ejected from the mold, showcasing the fine details.
Step 7: Post-processing
After the part is ejected, some finishing steps may be necessary. This could include trimming excess material, sanding, painting, or assembling parts. Any leftover plastic or flash (excess material) is carefully removed.
3. Advantages of Injection Molding
Injection molding has several key advantages that make it a preferred choice for mass production:
- High Efficiency: Injection molding allows for rapid production of high volumes of parts with consistent quality, making it ideal for industries requiring bulk manufacturing.
- Cost-effective: While the initial investment in molds and equipment can be high, the cost per part decreases significantly with large production runs.
- Precision and Consistency: Injection molding can produce parts with tight tolerances and high precision, which is crucial for applications such as medical devices and automotive parts.
- Design Flexibility: Injection molding allows for complex geometries, intricate details, and a wide variety of material choices.
- Low Waste: The process is highly efficient, with very little material waste. This makes it a more sustainable choice for manufacturers.
4. Industries That Benefit from Injection Molding
- Automotive Industry: Injection molding is extensively used for producing automotive parts like bumpers, dashboards, and interior components.
- Electronics: Electronic housings, connectors, and components like smartphone cases and battery housings are commonly produced via injection molding.
- Medical: Injection molding is ideal for medical devices like syringes, surgical instruments, and diagnostic equipment.
- Consumer Goods: Toys, kitchen appliances, and packaging materials are often made through injection molding.
- Aerospace: Parts like fasteners, brackets, and housings for the aerospace industry also benefit from this process.
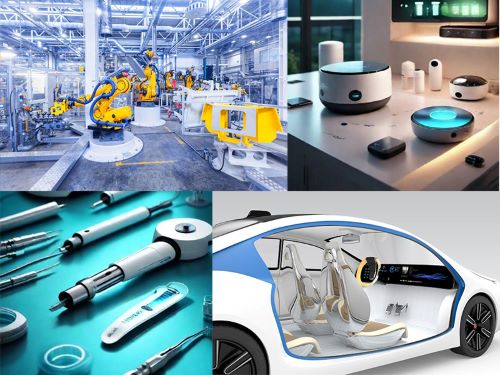
Application Areas
5. Why Choose TXS for Your Injection Molding Needs?
At TXS, we specialize in providing high-quality injection molding solutions for industries ranging from automotive to medical devices. With over 20 years of experience in precision mold making, material development, and production, we ensure the highest standards in every step of the injection molding process. Our team works closely with customers from product development to mass production, ensuring that every part meets your specific requirements for quality, performance, and cost-efficiency.
- State-of-the-art Equipment: We use cutting-edge injection molding and injection mold manufacturing machines from top manufacturers like Germany, Japan, and Switzerland, ensuring high precision and efficiency.
- Certified Quality: We adhere to strict quality control measures, including certifications for medical devices(LRQA: ISO 13485),automotive parts(LRQA: IATF 16949) ,other industries parts(LRQA: ISO 9001) , to guarantee that every part meets international standards.
- Global Expertise: We have extensive experience exporting to the U.S., Canada, Japan, and Europe, and can serve clients worldwide with tailored solutions.
6. Conclusion
Injection molding is a powerful, cost-effective manufacturing process used across various industries to create high-quality, precise parts. Understanding the process is essential for anyone involved in product design, development, and manufacturing. Whether you’re looking to create parts for electronics, medical devices, or automotive applications, injection molding offers unmatched precision, efficiency, and scalability.
At TXS, we can help bring your product designs to life with reliable injection molding services that ensure quality, cost-effectiveness, and on-time delivery. Contact us today to learn more about how we can assist you in your next project.
Four Elements of Injection Molding